Sign in to follow this
Followers
0
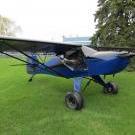
tubing wall for kitfox 3 1050
Started by
TJay,
6 posts in this topic
Create an account or sign in to comment
You need to be a member in order to leave a comment
Sign in to follow this
Followers
0