Sign in to follow this
Followers
0
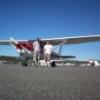
tailwheel spring bolts?
Started by
High Country,
11 posts in this topic
Create an account or sign in to comment
You need to be a member in order to leave a comment
Sign in to follow this
Followers
0