Sign in to follow this
Followers
0
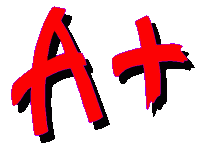
MGL E-1 EMS setup
Started by
dholly,
12 posts in this topic
Create an account or sign in to comment
You need to be a member in order to leave a comment
Sign in to follow this
Followers
0