Sign in to follow this
Followers
0
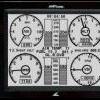
Forging ahead...spar tubes and fittings
Started by
Tree top pilot,
9 posts in this topic
Create an account or sign in to comment
You need to be a member in order to leave a comment
Sign in to follow this
Followers
0