Sign in to follow this
Followers
0
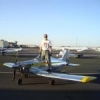
Grove gear geometry question
Started by
lostman,
19 posts in this topic
Create an account or sign in to comment
You need to be a member in order to leave a comment
Sign in to follow this
Followers
0